High Speed Cutting - HSC
Identification of the Lines of Research and the Project
In the area of product manufacturing, SCPM works with the development of research projects that consolidate Manufacturing Technology at High Speeds – HSC (High Speed Cutting) Technology in Brazilian companies within the aeronautic, aerospace, automotive and consumer goods sector.
The development of this Technology by individual industries has become enviable because there are large restrictions to its application. For instance, it requires a restructuring of the productive process based on all of the factors that influence the manufacturing process.
In addition to this, since it is a technology that is still being developed, there is a dearth of qualified professionals and technical information to fulfill the needs of the market. This gives the research institutions of the country a fundamental role in accelerating this application.
Given this situation, although HSC Technology is still in the early stages of development, SCPM has accumulated know-how in its application and integration into the CAD/CAM/CNC chain, working in various areas and presenting the following projects:
- Development and analysis of new methodologies of toolpath interpolation, particularly Polynomial and NURBS Interpolation;
- Studies of the factors related to the full integration of the CAD/CAM/CNC chain in the area of HSC Technology;
- Acquisition and treatment of data in manufacturing with HSC technology.
Among the projects developed by SCPM in the manufacturing area, the major emphasis is in the development and analysis of new toolpath interpolation methodologies, such as Polynomial and NURBS interpolations.
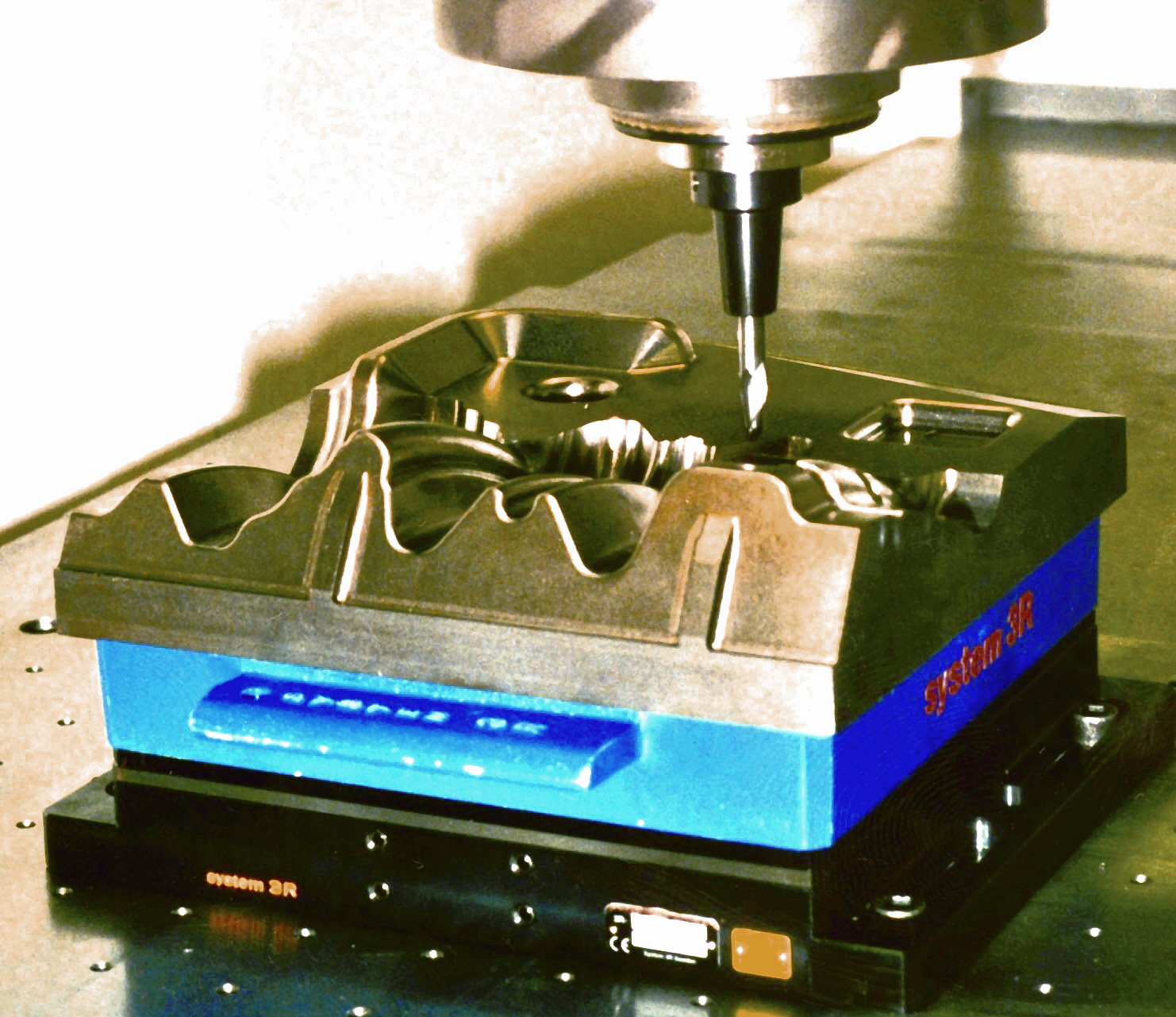
Context and Relevance
Within the CAD/CAM/CNC chain applied to product development, the paths that the tools follow, the creation of the NC program and, consequently, the manufacturing of a product, can be represented by various interpolation methods.
Each interpolation method provides its own characteristics to the NC program, and performs differently in HSC Technology
In traditional manufacturing, the toolpath interpolation methods are practically ignored as resources, making linear interpolation the standard due to its mathematical simplicity.
However, in HSC Technology, where the demands for higher speeds are greater, the linear interpolation method creates various limitations. This has resulted in the reconsideration of the importance of toolpath interpolation methods in the creation of the NC program.
This can be demonstrated through a test realized at SCPM to verify the behavior of the real feedrate in function of the increase in the programmed feed rate.
It can be observed that for a programmed rate of 1000 mm/min, the real rate remains constant. However, as the programmed rate increases, variations in the real rate become more accentuated along the complex surface areas.
Among these new methodologies, NURBS interpolation, in which the toolpath is represented by curves based on mathematical models, allows for a more precise toolpath and has become a solution for manufacturing with HSC Technology.
Due to these results, this project aims at characterizing and evaluating the use of different interpolation methods, such as Polynomial and Nurbs interpolation, in high speed manufacturing. The ultimate goal is to contribute to the implantation and restructuring of this productive process in the national industry.
Duration
This project began in 2001 with the approval of the Foundation for Research Assistance in the State of São Paulo (FAPESP) for the Thematic Project 00/02962-4 – Manufacturing Technology with High Speed Cutting.
Current stage of development
Currently this project has already acquired knowledge in the following areas:
- Knowledge on the influence of toolpath methodology in the creation of the NC program and, consequently, its influence on high speed manufacturing;
- Studies on the influence of the types of Interpolation (Linear, Circular and Polynomial) on the high speed manufacture of complex surfaces in regards to lead time, real rate and the accuracy of the final geometry;
- Studies on the resources of the Siemens 810/840D command in the generation of toolpaths;
- Studies on the methods of acquiring real manufacturing rates.
Among the future activities to be carried out, we can highlight:
- Prove the efficiency of NURBS interpolation in representing the toolpath in the manufacture of molds and dies.
|